Globe Valve
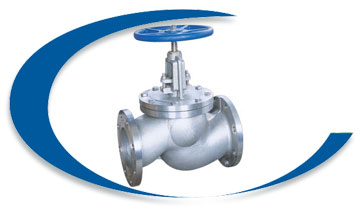
A Globe valves is a linear motion valve and are primarily designed to stop, start and regulate flow. The disk of a Globe valve can be totally removed from the flow path or it can completely close the flow path.Conventional Globe valves may be used for isolation and throttling services. Although these valves exhibit slightly higher pressure drops than straight=through valves (e.g., gate, plug, ball, etc.), they may be used where the pressure drop through the valve is not a controlling factor.Because the entire system pressure exerted on the disc is transferred to the valve stem, the practical size limit for these valves is NPS 12 (DN 300). Globe valves larger than NPS 12 (DN 300) are an exception rather than the rule. Larger valves would require that enormous forces be exerted on the stem to open or close the valve under pressure. Globe valves in sizes up to NPS 48 (DN 1200) have been manufactured and used.
We are an ISO 9001:2008,ISO 9001-2008, ISO 14001-2004, OHSAS 18001-2007, NSIC-CRISIL, EEPC, and QA-UKAS (ISO 9001-2008), SSI Certified company that follows total Quality Management System. and have been recognized as one of the world’s leading stockists and manufacturer of quality metals for over two decades and are committed to quick responses, unsurpassed quality, competitive pricing, reliable deliveries and an exhaustive inventory.Globe Valves are extensively employed to control flow. The range of flow control, pressure drop, and duty must be considered in the design of the valve to avert premature failure and to assure satisfactory service. Valves subjected to high-differential pressure-throttling service require specially designed valve trim.Generally the maximum differential pressure across the valve disc should not exceed 20 percent of the maximum upstream pressure or 200 psi (1380 kPa), whichever is less. Valves with special trim may be designed for applications exceeding these differential pressure limits.
Globe valve Specification
Type | Globe Valve |
Standred | DIN 3352 F5 |
Material | Industrial-grade steel, carbon steel, stainless steel, alloy steel and special steel, A105, A182, F304, F316 |
Size | 1/2"-2" |
Diameter | 1”to13” |
Order | Accept custom order |
Construction of a Globe valve
The principal variation in Globe-valve design is in the types of discs employed. Plug-type discs have a long, tapered configuration with a wide bearing surface. This type of seat provides maximum resistance to the erosive action of the fluid stream. In the composition disc, the disc has a flat face that is pressed against the seat opening like a cap. This type of seat arrangement is not as suitable for high differential pressure throttling.
Advantages and disadvantages of Globe valves
Advantages:
• Good shutoff capability• Moderate to good throttling capability
• Shorter stroke (compared to a gate valve)
• Easy to machine or resurface the seats
• Available in tee, wye, and angle patterns, each offering unique capabilities
• With disc not attached to the stem, valve can be used as a stop-check valve
Disadvantages:
• Higher pressure drop (compared to a gate valve)• Requires greater force or a larger actuator to seat the valve
• Throttling flow under the seat and shutoff flow over the seat
Globe valve Components
Globe valves have a very distinct globe shape. The disk, valve stem, and the hand wheel are the moving parts in the valve body. The body is available in three different designs depending on the application as well as three different types of disks.
Body Construction: Due to the angles in the globe valve body there is a high level of head loss. Head loss is the measure of reduction in the total head of liquid as it moves through the system. Total head loss can be calculated by summing the elevation head, velocity head and pressure head. While head loss is unavoidable in fluid systems, it is increased by obstructions and discontinuities in the flow path such as the S shape of the globe valve design. The body and flow pipes are rounded and smooth to provide system flow without creating turbulence or noise. To avoid creating additional pressure losses at high velocity the pipes should be a constant area. Globe valves are available in three main body types (although custom designs are available as well): angle design, Y-shaped, and Z- shaped.
Bonnets: retain the pressure in the valve by acting as a cap or cover for the body.
Trim: Trim consists of the disk and seat ring. The disk is lowered onto a matching horizontal seat located in the center of the valve. The disk goes into the seat ring to stop flow through the system. The disk is a plug with a float or convex bottom. The location of the valve disk in relation to the valve seat allows or restricts flow.Ball disks fit into a tapered, flat-surface seat. The ball disk is best used in low pressure, low temperature systems. They can be used for throttling services but they are best used to start/ stop flow.
Composition disks are replaceable disks designed with a hard, nonmetallic insert ring on the disk. They are best used in steam and hot water systems because they resist erosion. Composition disks are also resilient enough to close on solid particles without damaging the valve.Plug disks are long tapered disk available in a variety of specific configurations. The plug disk provides better throttling than ball or composition disks.
Disk and Stem Connections The stem connects the hand wheel and the disk. It's threaded and fits into the threads in the valve bonnet. The constant turning of the stem to open or close the valve may cause a weakening in the glad seal (packing). There are two possible methods for connecting the disk and stem.
T-slot construction: The disk slips over the stemNut design: The disk is screwed into the stem
Design Tip: Take care to not screw the valve shaft too far because there is a possibility it could damage the seating surface. For quick-acting globe stop valves, the stem is placed so the disk closes in the same direction as the fluid flow. Closing the valve is impeded by the kinetic energy of the media but opening is faster and easier.
Seats: The seat of a globe valve is either integrated with or screwed into the valve body. Most globe valves have a seating arrangement that provides a seal between the stem and bonnet called a backseat. The backseat prevents pressure from building against the valve packing because the disk rests against it when the valve is open. The disk to seat ring contact is close to a right angle, reducing the amount of seat leakage because a tight seal can be formed. Many globe valves feature top entry to the plug and seat to allow for easier servicing of the internal parts while the valve remains in-line.
Valve Actuator: The valve actuator operates the stem and disk to open and close the valve. There are several types of actuators depending on the needs of the system such as the torque necessary to operate the valve, speed and the need for automatic actuation. Manual/ hand operated actuators use a hand-wheel or crank to open or close the valve. They are not automatic but offer the user the ability to position the valve as needed. The hand-wheel can be fixed to a stem or hammer which allows for the valve to be pounded open or closed if necessary. In manual globe valves, the stem screws the plug in to close or shut the valve. The threaded system is slower and not as smooth as an automated system, but it does offer easy operator control.
Packaging Of Globe valve
1.Hessian / PVC Cloth Bundles with PVC Box Strap or Hexagonal Bundles2.Wooden Crate
3.Wooden Box made of treated wood or Plywood sheet
4.Bundles (hexagonal)
5.Crates (steel/wooden)
6.Special Crates
Application Of Globe valve
1.Food Industries2.Water Industries
3.Oil & Gas Industries
4.Automotive Industries
5.Ship Building Industries
6.Petro-Chemical Industries
7.Engineering Cement Industries
8.Transport Industries-Rail and Road
9.Chemical & Pharmaceutical Industries
10.Construction Industries / Building Systems